Your boiler and in-floor heat experts
- Sr Perspective
- Aug 1, 2019
- 5 min read
‘If you have a big problem and you want it fixed right, call these guys.’
If you are having trouble with your current boiler, in-floor heat system or any hydronic system in your home or business, Koegel Plumbing and Heating Solutions has the experience and knowledge to assess, explain and fix the problem.

Kurt and Dana Koegel own and operate Koegel Plumbing and Heating Solutions, which serves west central Minnesota. Photo by Jim Palmer
Koegel Plumbing and Heating Solutions, based in Miltona (near Alexandria), is owned and operated by Kurt and Dana Koegel. Kurt specializes in hydronic heating (boilers) with more than 30 years of experience. The Koegels have been helping people with their hydronic needs in west central Minnesota since 2012. The Koegels believe in upfront pricing and offering clean, courteous and professional service.
This article features two of their recent success stories…
Corrine Hayden, of Fergus Falls, called Koegel Plumbing and Heating Solutions to take a look at her boiler.
“I actually learned about Koegels by reading about them in Senior Perspective a couple of years ago,” said Corrine. “My house had a 1938 boiler and the article caught my attention.”
Corrine’s 80-year-old boiler had served its purpose over the years but was not very efficient and was starting to show its age.
“I had Kurt come over, and he knew the whole history on the boiler right away,” she said. “I was very impressed.” “The boiler was at the end of its life,” said Kurt, “The boiler sections were starting to spread apart because the metal was warping, and it was letting carbon monoxide gas escape into the basement. The boiler was also covered in asbestos.”
Corrine hired a special contractor to remove all of the asbestos, and then Koegel Plumbing and Heating Solutions went to work.
“Corrine’s basement floor was absolutely spotless when we arrived,” said Kurt. “We could compare it to a hospital operating room. The challenge was to upgrade her heating system with something more efficient, remove this monstrous old, rusty boiler and at the same time keeping the basement and house as clean as we found it.”
They started by laying down two layers of cardboard around the old boiler and covering the painted basement steps and surrounding floor with canvas drop cloths. Then they started removing the old boiler.
“We broke the boiler down into sections, catching the old dirty water and vacuuming the soot as we went along,” said Kurt. “Once the boiler was removed and the area cleaned we installed a wall-hung high-efficiency Laars boiler that was about one-quarter the size of the old boiler. We were able to keep the house as clean as we found it, and Corrine now has a much more efficient boiler.

Before (left) and after (right) of Corrine Hayden’s boiler replacement. The new boiler is much more efficient and takes up much less space in Hayden’s basement. Contributed photo
“It was a dirty, messy job,” said Corrine. “They did a tremendous job and cleaned it all up when they were done. The new system is mounted it on the wall and is much more efficient. I was very happy with them. I would definitely recommend Koegels to anyone.”
Another area of expertise for Koegel is radiant or in-floor heat. Meredeth Lake, of Alexandria, was having trouble with her in-floor heating system. After calling a couple of other service companies to take a look at it, she was advised to call Koegel Plumbing and Heating Solutions.
“The others didn’t get it, but Kurt got it right away, and he explained to me why it wasn’t working properly,” she said.
“Meredeth’s house had in-floor heating throughout the house, and the builder put oakwood flooring on top of the concrete,” said Kurt. “She liked the idea of having warm floors, but she was using a lot of propane.”
“It was burning through a whole bunch of propane,” said Meredith.
When Koegels arrived at the house, they noticed something right away.
“There was no snow around the entire perimeter of the house, and right next to the foundation of the house outside there was actually soft mud, even though it was 0 degrees outside,” Kurt said. “The foundation of her home was not completely insulated. It appeared that there was insulation underneath the tubing in the floor itself, but with the help of our thermal camera we could see heat escaping through the uninsulated block foundation wall to the outside of the home. We used our thermal camera to identify how the tubing was running, and it also helped us determine the massive heat loss occurring around the perimeter of the home.”
The second challenge identified was an air-sensing thermostat used for the in-floor heating system.
“With this type of thermostat, the heating system would have to heat the entire floor as well as the ambient air before the call for heat to the thermostat would be satisfied,” said Kurt. “This caused the rooms to overheat and use a lot of propane. We replaced it with a slab-sensing thermostat that would be satisfied when the slab foundation itself reached a preset temperature.” And finally, a third challenge.
“The system had three heating sources—an electric forced hot air furnace, an electric boiler used to heat the radiant in-floor system and an LP (propane) boiler as a back up. This heating system initially used the electric boiler to heat the water for the radiant in-floor tubing. The electric boiler eventually died, and the LP boiler became the primary source of heat for the in-floor system.”
Kurt explained all the different options available along with the pros and cons of each before arriving at a solution together with Meredith.
“We ended up removing the electric boiler that was no longer functioning,” said Kurt. “We installed new manifolds, installed a slab-sensing thermostat, filled the system with new antifreeze and kept the existing LP boiler.”
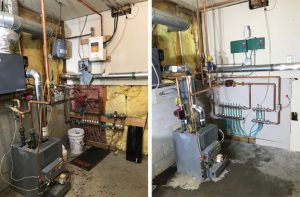
Meredith Lake’s in-floor heat system was repaired and improved as seen in these before (left) and after (right) photos. Contributed photos
They changed the piping layout to the boiler, which made it more efficient, and tweaked the system so that the radiant in-floor system would keep the floors warm, but would not be the main heat source of the house.
“Then we worked with Shawn from Jim’s Electric to rewire the system so that the electric forced hot air system would be their main heat source that ran off of off peak electric,” he said. “As a backup to the electric furnace, we placed a hot water coil in the duct work that ran off of the rehabilitated system. Now, during off-peak times when the electric furnace was turned off, the gas boiler would heat the house through the duct work of the forced air furnace in addition to the radiant in-floor system.”
With these changes the heating system in Meredeth’s home is now more energy efficient, saving her money, while still keeping her home warm and comfortable.
“Now the in-floor heat is much more efficient and easy to use,” she said.
And after the project was done, Kurt even went the extra mile to help Meredith with another issue.
“I had a smoke detector that kept going off, and Kurt took care of that, too,” she said.
Meredith said that she was so pleased with the service and results provided by Koegels that when she saw their van cruise by weeks later, she followed it.
“I tracked them down so I could give them a hug,” she smiled. “If you have a big problem and you want it fixed right, call these guys.”
Koegels can do the big jobs (like churches) and they also enjoy the small jobs… and anything in between. They offer full-service plumbing and hydronic heating services throughout west central Minnesota.
To get a low-cost review of your system, including diagnostics and options, call 320-766-6767 or email kurt@koegelsolutions.com. To learn more about Koegel Plumbing and Heating Solutions, visit ww.koegelsolutions.com.
This is a paid business profile. If you would like to learn more about promoting your business in the Sr. Perspective with a business profile, call Jim at 320-334-3344.
コメント