One of a kind guy... and wood creations
- Sr Perspective
- Dec 16, 2024
- 5 min read
Updated: Dec 17, 2024
by Larry Magrath
There’s a reject shelf in Pete Bader’s one-stall wood shop in Tracy, Minn. It holds the more discernable remnants of lathe-turned wood bowls, plates, and saucers that didn’t make the cut. Too rough. Too thin. Cracked. Broken.

Not too far away are totes full of the turned pieces that did make the cut and are awaiting a new home. Some are small and may be put to use one day catching the pocket change and car keys at the end of the day on a shelf. Others are large enough to serve a salad in or an attractive display of fruit, one-of-a-kind. Each is as unique as the tree it came from, adroit hands coaxed the piece into artful existence.
“I enjoy watching the grain of the wood pop out at me,” Bader said. “I’m surprised at myself sometimes. They are unique. I can’t even make another one exactly like it. If you give one of these, you know you’re giving something that nobody else can do just like it.”
In 2006 retirement drew Bader, now 85, and wife Dianne to Tracy to be closer to sons Dean and Glenn and their families in Marshall. They spent their life in Carson, N.D. operating a gravel-hauling business. Another son Travis and his family live in Gilbert, Ariz., and his daughter Kristie Taarud and family live in Farmington, Minn.
Nowadays, his side of the garage doubles as his wood shop and he recently erected a partition between the two car stalls in the endless battle to keep the dust contained. You can never collect enough of the dust, he mentions with a laugh.
He considers himself an experienced hobby woodworker, having made many household items like coffee and end tables, kitchen cabinets and lamp pedestals. He started with lathe work seven years ago when a friend was getting out of that type of work and offered him a lathe. He figures he’s turned out hundreds of pieces since then.
“I didn’t know the first thing about it, but I learned,” Bader said.
His kids, grandkids and friends got their fill of the pieces and for the last two summers he could be found at the Marshall, Slayton, and Balaton farmers markets. He’s also attended a market in Farmington, while there visiting their daughter’s family and Tyler was a new stop this fall.
“This is not supposed to be a business. It’s supposed to be a hobby,” Bader said. “I enjoy doing it but after a while my wife said, ‘Well you can’t keep putting them in the boxes. You got to get rid of them. You need to get some money back so you can buy more stuff.’”
A demonstration of his skills on the lathe is loud and dusty but mesmerizing and it doesn’t take long to turn what looked like a hunk of firewood into an improbable likeness of a bowl. Bader dons his standard safety gear including an apron, ear plugs, and face shield. He recently added a respirator in a battle with the dust of Walnut which he says has deleterious effects on the lungs. It’s toxic.
He has worked with a variety of wood including Walnut, Ash, Maple, Locust, Mesquite, Mulberry, and Ironwood.
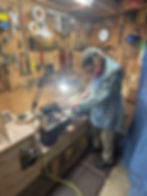
His hands have suffered serious injury but he’s sticking with it for now. He discovered a flaw in one of his lathes the hard way.
“Well, they said they could send the new parts out, but they couldn’t send a new finger out,” he said. “It’s alright. You know you can’t quit because of that. Not when you enjoy it.”
Bader only quits when the piece he’s working on reveals itself.
“One time I was cutting out a bowl and a perfect heart figure came out on the bottom, and I wasn’t going to quit there but after seeing that I quit right then because it was so beautiful. Of course, that bowl sold instantly.”
The bowls with a live edge sell the best. They represent a sort of artsy imperfection that tips the viewer off that the piece is closer to art and nature than it is to manufacturing.
Toward finding an alternative, he’s been investigating a CNC (Computer Numerical Control) machine and recently received a demonstration.
“I’m not too sold on this because it would take the fun out of doing it. The machine would be doing it,” Bader said. “I would be doing the computer stuff.”
Learning how to get the result he wants is challenging. Some of the learning is industry standard practices and tools and some is the challenge of creating his own jigs. He’s a regular user of YouTube and the community of woodworkers who teach him how to work through issues. Keeping tools sharp is paramount.
“Some tools are so hard to understand it takes me a long time. Like this rough gouge. They tell you, you have to ride the bevel so you don’t get a catch when you’re working with your wood. And it took me quite a while to finally figure them out, what it meant to ride the bevel just right,” Bader said. “It’s a good tool once you master it to get what you need inside your bowl.”
The pieces are finished with a matte oil finish safe for foodstuff or a glossy finish. Food safe bowls can be wiped clean and even immersed in water for cleaning and then dried. Metal utensils are to be avoided of course.

Experimenting with the process has led the way to where he is today. One bowl he showed off is particularly heavy. He made it from Ironwood that came to him through a friend who picked it up in Arizona. It’s very dense and as the name suggests heavier than other wood most are familiar with. His initial attempt at cutting it failed, then YouTube provided the answers he needed. He ended up not being too fond of the wood and doesn’t plan on working with it again.
Like any decent shop owner knows, he has more tools than he needs most of the time but then you never know what you might need.
One of his more unique turned pieces mixes wood varieties in a way that seems unlikely, a bowl with a base color brown Mulberry followed by Walnut then Locust, then Walnut again. Soup would be right at home in this piece. To that end he made a jig to cut the joining edges at a 35-degree angle because a flat mating would not work. Glue holds them together then more lathe work to smooth off with tools and sandpaper.
Bader signs his pieces with a brand burned in the bottom: Pete’s Woodworking God Loves You John 3:16 Pete Bader.
“I think it’s so important to get that message out to people because that’s my belief,” Bader said.