‘Loomers’ continue the age-old craft
- Sr Perspective
- Sep 1, 2021
- 5 min read
By Vivian (Makela) Sazama
Weaving rugs, sometimes called “looming” since the rugs are woven on a loom, has been a craft practiced in many forms for centuries. Several residents in the Menahga-Sebeka area are practicing loomers. In this article, they share their looming experiences...

Larry and Judy Huotari of rural Sebeka began their looming experience 8-10 years ago by purchasing a loom from Olavi and Siirkka Seppala of Menahga. The Seppala’s had acquired the loom from a Lapinoja family and at that time they figured the loom was over 100 years old. The age could be evidenced by the way the loom was constructed, using wooden pins and dowels, as nails were possibly in short supply.
Judy first became interested in looming through her mother’s uncle and aunt, who were both blind. They would receive help by asking someone to sort the material colors they used, but then would do the weaving themselves, selling them as a means of supplementing their income. Judy said she has sold a few rugs, but mostly donates them or gives them as gifts.
Looming has been a learning experience for the Huotaris. Setting up the warp, or the strings through which the strips of material are woven, has been the most challenging, they said.
“I made this piece to wind the string on first, then transfer it onto the loom, to make it easier,” said Larry, pointing to a wooden bar off to the side of the loom. Larry showed how the different levers on the loom tighten the warp strings. “It’s got to be tight, so the rugs last a long time!”
For rug material Judy prefers using old sheets that she tears into strips and sews together in a half moon shape, then wraps the strips into a ball. Larry said they find a lot of their sheets at thrift stores.
The Huotari’s loom came with six pedals, but they are currently only using four. The extra two pedals are for adding decorative touches to the rugs, such as flowers and other designs, something that Siirkka had done, but which Judy has not tried yet. After the rugs are at a length that they want, Judy then adds a filler strip of other material before continuing with the next rug. Larry said after eight or nine rugs are done, they take the roll of rugs off the loom and Judy cuts through the middle of the filler strip, after which the strings are then tied off.
At first they set up the loom in their garage, but then built a “rug house” with double doors in order to get the loom inside. There is a heater so they can weave spring, summer and fall; but the Minnesota winters can be a bit too cold, Larry said.

Gerald (Jerry) Kumpula of Menahga began his looming experience about seven years ago, when it was discovered that his grandmother’s loom was being stored in a cousin’s garage. The loom had been passed on to his mother in the 1940s after his grandparents had moved to town from their farm.
Jerry’s family house burned down when he was 16 and he thought the loom had burned with it, but the loom had been given to an uncle, and then eventually passed on to his cousin. After many decades of disuse, Jerry restored the loom and made it operational once again.
Jerry said originally the loom’s heddles, through which the strings, or warp, are strung were all hand tied strings, not metal as most looms have. He replaced the hand tied heddle with a metal one and did some other modifications as needed, including putting in a new metal reed which pounds the rugs into place. “The old one was all rusted out,” he said.
Jerry recommended that people watch videos by Elizabeth Wagner on how to use a rug loom, saying she is very thorough in explaining everything from start to finish. To make it easier to string the warp, Jerry built a wheel instead of a “tree,” which loomers usually use.
In addition to rugs Jerry has also made sauna mats and table runners. The longest rug Jerry made and sold was 9 1/2 feet. One that one he used men’s dress pants that he found at a thrift store.
Each loomer seems to have their own way of sewing the strips of cloth together before rolling into a ball. Jerry sews his strips at an angle, then trims the excess.
Jerry commented on how his grandmother Mary had woven a woolen blanket for each of her 10 children, sewing two pieces together. He said she had raised the sheep, cleaned, carded, dyed and spun the wool, then woven on this very same loom.
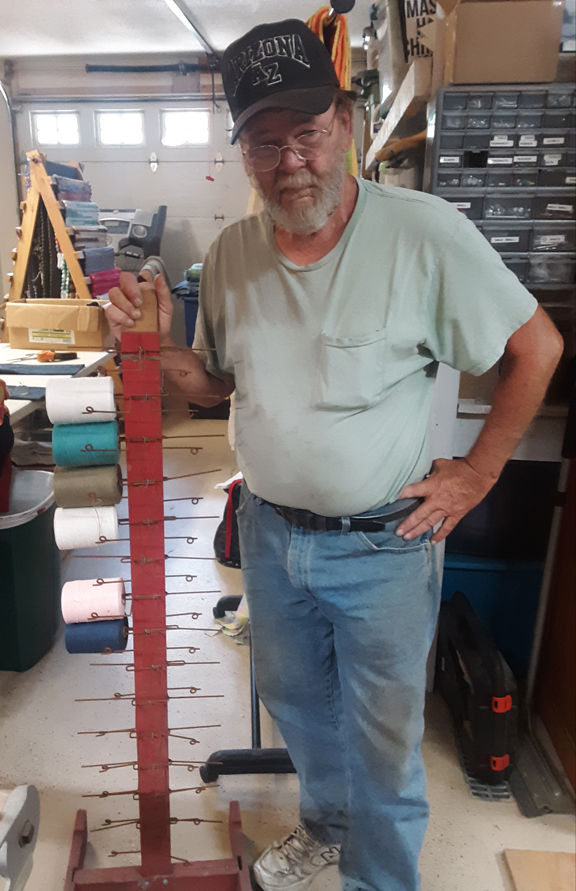
Bob Seikkula of rural Menahga has a collection of studio rug looms, all which originally came from the Newcomb Loom Company of Davenport, Iowa. That company operated from 1890 to 1930. His looms each have a serial number stamped on, with three of his looms having Y2624, X2172 and X2386. One that he thinks is the oldest has 14958 stamped on it. That loom has a gear box and uses pulleys and side fly shuttles, rather than foot peddles. It is possible that this is one that Charles Newcomb, an Omaha, Nebraska contractor and wheel maker who founded the Newcomb Loom Company, developed prior to setting up his factory in Iowa.
Initially Bob had only his mother’s two-peddle Studio loom stored in his heated garage.
“Mother bought the loom from Sylvia Mertala in about 1961 or 1962,” Bob said. Sylvia had purchased the loom brand new, and according to several catalogs, Bob found in his mother’s basement, the price was about $150 to $175. After Bob’s wife, Maria, died in 2017, Bob went on YouTube to learn about looming. “I got an idea on how it’s supposed to be done. I learned through trial and error,” Bob said. Bob used a “tree” to aid in wrapping the string for the warp.
“The tree dedicates the pattern and how you are going to put the strings onto the loom.” Bob said. “Typically, you’d think you start at the top, but no, you have to start at the bottom and work your pattern up. It was a learning curve, the first time I strung it,” he laughed.

Over the last few years Bob added more looms to his collection. He bought one six-peddle loom from Deb Lenzen of Menahga, which can be used to add intricate patterns to the rugs, something Bob hasn’t tried yet.
For material Bob has used towels, flannel sheets, old living room drapes, chenille bedspreads and even plastic table cloths, most of which he finds at thrift stores. He has sold a lot of rugs at craft fairs and swap meets, some even in Arizona over several winters. Most recently he has his rugs in a gift shop in Park Rapids.
Though looming seems to be becoming a lost art, it’s still being preserved in the Menagha-Sebbeka area. Bob’s granddaughter Kate has shown an interest in learning to loom. He has plans of passing on a loom to each of his three granddaughters one day.
Comments